Understand the structural, functional, and application differences between standard and heavy-duty workbenches to ensure safety, efficiency, and long-term durability.
What’s the Difference Between a Workbench and a Heavy-Duty Workbench?
1. Definition
Standard Workbench:
- Designed for light to medium-duty tasks.
- Commonly used for assembly, inspection, light repair, and packing.
- More affordable, lighter, and easier to move.
- Typically made with lighter materials for both the frame and the surface.
Heavy-Duty Workbench:
- Built to withstand high loads, frequent impact, and support heavy machinery.
- Ideal for mechanical assembly, metalwork, large repairs, and industrial use.
- Stronger frames (thicker steel, welded joints, reinforced supports).
- Surface materials are more durable and have higher load capacities.
2. Construction & Design Differences
- Standard Workbench: Assembled with bolts, uses thinner materials. Easy to install or disassemble.
- Great for light-duty lines or labs. Low cost, lightweight, and flexible.
- Heavy-Duty Workbench: Built with welded steel frames, thicker materials, and industrial-grade construction. It requires a higher upfront investment but delivers a longer lifespan and superior durability for tough environments.
3. Use Case Scenarios
- Standard Workbench: Electronics assembly, light repairs, inspection, packaging.
- Heavy-Duty Workbench: Mechanical work, large equipment maintenance, metal fabrication, or any high-force tasks.
When choosing a bench, think about what you need.
Think about how heavy your tools and materials are. Also, consider how often you will use them, whether they will endure impact, how much you’re willing to spend, and how long you need them to last.
When to Choose a Standard or Heavy-Duty Workbench.
For occasional light tasks, a standard bench is cost-effective and practical. For frequent heavy tasks, a heavy-duty workbench is a safer and longer-lasting investment.
What’s the Best Height for a Workbench?
There’s no one-size-fits-all answer. The ideal height depends on your height and the task at hand.
General rule: Measure your standing elbow height and set the workbench 4–6 inches (10–15 cm) below that. This helps reduce strain on your neck, shoulders, and lower back.
Recommended Heights by Task Type:
Light or precision work (assembly, drafting): 36–39″ (91–99 cm)
General work (cutting, hammering): 34–36″ (86–91 cm)
Heavy-duty work (pounding, forceful tasks): 28–34″ (71–86 cm)
For flexibility, many modern benches offer adjustable-height options, ideal for multiple users or task types.
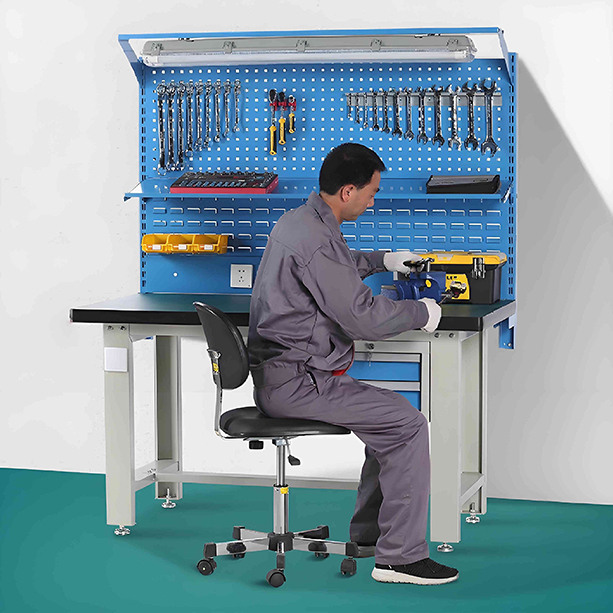
How Much Weight Can a Workbench Hold?
Comparing Load Capacity:
Standard workbench: 250–500 lbs (113–227 kg)
Heavy-duty workbench: 1000+ lbs (450+ kg), some models up to 2000–5000 lbs (900–2250 kg)
Important Elements That Impact Load Capacity:
Frame Material:
Steel – Ideal for industrial use, highly durable
Wood – Suitable for light-duty applications
Aluminum – Lightweight, but limited load-bearing capacity
Surface Material:
Solid wood (e.g.maple, beech) – Robust and sturdy
Steel – Perfect for heavy-duty tasks
MDF/particleboard – Budget-friendly but less durable
Structural Design:
Reinforced beams or cross-bracing improve strength
Floor anchoring and thick legs increase stability
Larger surfaces help distribute weight, but need structural balance
What Are the Safety Rules for a Workbench?
Safety is key to preventing accidents, protecting equipment, and maintaining efficient workflow. Here are essential safety tips, especially for benches with drawers or storage compartments:
1.Prevent Overloading: Avoid placing excessively heavy or unstable items on the bench.
2.Stable Placement: Set the bench on a level, solid surface. Use adjustable steel feet if needed.
3.Respect Load Limits: Never exceed the weight capacity of the bench or its drawers.
4.Even Weight Distribution: Spread weight across the surface to prevent tipping.
5.Keep Drawers Closed: Open drawers can pose tripping hazards or cause imbalance.
6.Use Locking Drawers: Choose benches with self-locking drawers for tools or valuables.
7.Regular Inspections: Check for loose bolts, worn parts, or damage regularly.
8.Keep It Clean: A tidy workspace reduces fire and trip hazards.
9.Ensure Adequate Lighting: Good lighting helps reduce errors and prevent accidents.
10.Organized Tool Storage: Avoid clutter—messy areas increase the chance of damage or injury.